The following situation arises often in practice: During the turning work, workpieces have to be machined both on the inside as well as outside. So far, it was necessary to carry out the two operations either on two machines or completely change the clamping devices, which is costly and time consuming. For this challenge, the RÖHM specialists succeeded at combining the mandrel and collet chuck in just one product.
The result is the new, patented Duplex clamping system. In the ideal case, changing from internal to external clamping is carried out quite simply without retooling or alternatively in just a few seconds by changing the clamping sleeve with the help of a bayonet lock. Besides elimination of the time consuming and costly clamping device changeover, the Duplex system is captivating by its precision and deformation-free clamping with concentricity and axial true-running of 0.01mm.
“That is because if no clamping element has to be changed, then no loss of precision can arise,” says RÖHM product manager Christoph Schauerte.
The other benefits in detail: Thanks to the complex construction, the Duplex system has low weight and a reduced overall height. There is uniform force distribution due to the surrounding clamping. No damage can occur to the surface of the workpiece thanks to the axially fixed clamping sleeve. Another typical RÖHM special feature: As required, the clamping sleeve blanks can be adapted individually to the workpiece and delivered vulcanised.
Conclusion: With the Duplex clamping system, RÖHM meets another requirement to be able to manufacture more effectively, easily and quickly. That way, the company offers its customers true added value in order to be able to meet the growing demand for cost-effectiveness, precision and short delivery times.
Internal and external clamping in one: The new Duplex clamping system from RÖHM
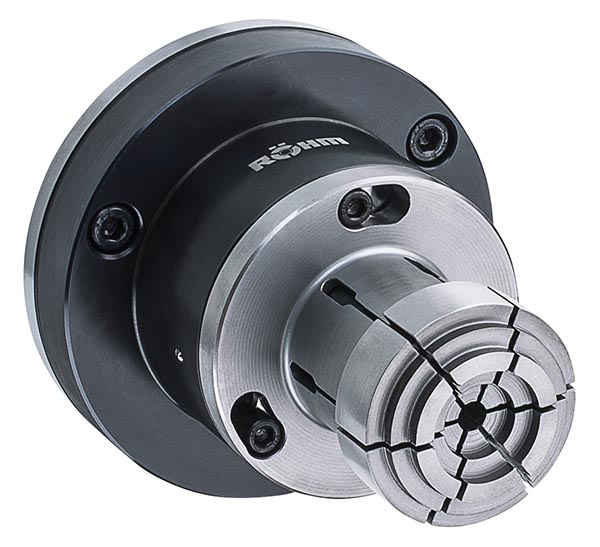